We are living in a world where artificial intelligence (AI) is transforming eve....
What is The Cost of Quality?
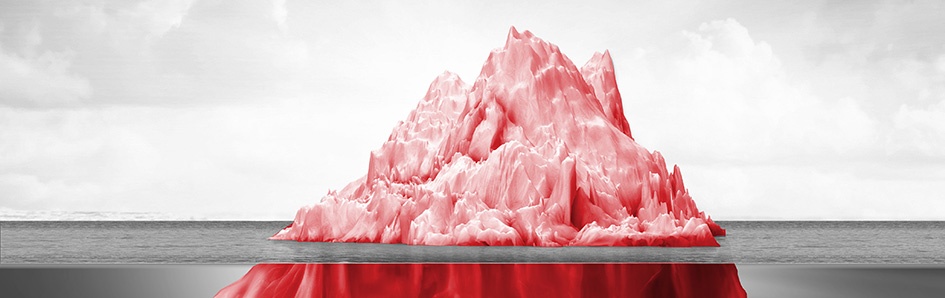
Almost all executives claim that they manage quality, but yet the need for corrective actions continues to grow. Imagine if we lived in a world where preventive actions are enough to have the desired products and services, and that spending for corrections would be unnecessary. Imagine if organizations didn’t have to spend money to improve their mistakes. Unfortunately, they do, and they call it the cost of quality.
Is the cost of quality related to the cost of undertaking quality initiatives, or not undertaking them? The term might sometimes confuse people in thinking that quality is a cost. However, experience shows that quality is only a drive that increases profits while lowering costs. According to the 3rd point of Deming’s 14 points for management, one should “cease dependence on inspection to achieve quality. Eliminate the need for inspection on a mass basis by building quality into the product in the first place.” He suggests that quality comes from process improvement and not from inspection. Practically, the cost of quality is also the cost that derives from not creating a quality product or service.
Let us first analyze why this term confuses people so much. The cost of quality measures the lack of quality, or the result of not improving the quality performance beforehand. Improving quality is highly important for organizations that want to achieve their objectives. Taking measures before the products or services are produced or offered lowers the risk of having a high cost of quality.
The cost of quality increases from several reasons such as not evaluating supplier quality which can lead to rework, loss, customer complaints and returns. In addition, if an organization does not calibrate its equipment it can lead to machine repair, which also increases the cost of quality. Unskilled employees can have a low performance leading to rework, which also raises the cost of quality related to labor for rework. All of the above mentioned reasons and many others such as environmental costs, repairing products, redesigning, re-testing, warranties, and so on can increase the cost of quality.
If the reason leading to such cost is prevented, the cost of quality would keep decreasing and preferably eliminated. Many actions can be taken to decrease the cost of quality and they include supplier quality evaluation, machine calibration, training the employees can decrease the costs related to labor for rework, providing work instructions, controlling materials used for production, and so on. All these actions are preventive actions which aim at reducing the cost of quality.
According to Philip Crosby, the cost of quality is comprised of internal and external failure costs that result from not meeting the requirements. In addition, cost of quality identifies two other cost areas and they include prevention which result from preventing non-conformance to requirements, and appraisal costs which include measuring, evaluating or auditing to check whether products and services were performed in accordance with set standards.
Organizations worldwide are implementing quality systems, tools and methodologies because quality commitment is crucial for the success of every organization. Managing quality usually means having a lower cost of quality, which is why many organizations engage in the process of continual improvement to secure their future. Organizations keep their customers satisfied and reduce the risk and cost of defective products through quality initiatives.
ISO has developed different standards which aim at improving quality in organizations. One of the most used ISO standard worldwide is ISO 9001 (Quality Management System - QMS). ISO 9000 family addresses various aspects of quality management for organizations who want to ensure that their products and services meet customer’s requirements. You may be wondering, how much does it cost to have an ISO 9001 certification? But have you thought about what is the cost of not having an ISO 9001 Certification?
PECB (Professional Evaluation and Certification Board) is a certification body for persons on wide range of international standards. It offers ISO 9001 training and certification services for professionals wanting to gain a comprehensive knowledge in quality management, its principles, core subjects and issues. This training suits quality professionals, project managers or consultants wanting to prepare and to support an organization in the integration of a quality management system throughout the organization. In addition, ISO 9001 training can also be followed by auditors wanting to perform and lead quality management certification audits, and staff involved in the implementation of the ISO 9001 standard.
ISO 9001 and Quality Management Trainings offered by PECB:
- Certified ISO 9001 Lead Implementer (5 days)
- Certified ISO 9001 Lead Auditor (5 days)
- Certified ISO 9001 Foundation (2 days)
- ISO 9001 Introduction (1 day)
Lorika Bina is the Transport, Telecommunications, and Energy (TTE) Product Manager at PECB. She is in charge of developing and maintaining training courses related to TTE. If you have any questions, please do not hesitate to contact her at training@pecb.com.