In the global marketplace, the varieties of available products that travel across borders are immense, from Japan to Canada, Germany to Russia, Australia to India, China to Austria, etc., and with high demands. Regardless, if the supplier is a corporation, small business, or private entity, there are different suppliers that sell products by claiming to comply with all the requirements, yet, many people die or get sick from unsafe products. Contemptibly, children are often the victims of unsafe products such as toys. According to Nationwide Children's Hospital around 3.3 million children were treated in ERs for toy-related injuries between 1990 - 2011. To make things worse, Consumer Product Safety Commission states that 1 child dies every 2 weeks as results of TV, furniture or appliance falling on him or her. Principally, this is a result of a product which enters a marketplace without meeting a set of regulations and standards.
In order to reduce the risk that is caused by unsafe products in the marketplace, ISO 10377 (Consumer product safety–Guidelines for suppliers) and ISO 10393 (Consumer product recall-Guidelines for suppliers) are the standards that need to be implemented. ISO 10393 provides an organization with sufficient information and tools that all suppliers’ can use to develop a product recall programme that will help them to reduce legal standing risks and to diminish health or safety risks to consumers. While ISO 10377 provides an organization with the practical guidelines on how to assess safety products from the design phase until the final phase of the disposal of the product. Moreover, these international standards have been developed in parallel to present the guidelines for the suppliers, as illustrated in figure 1:
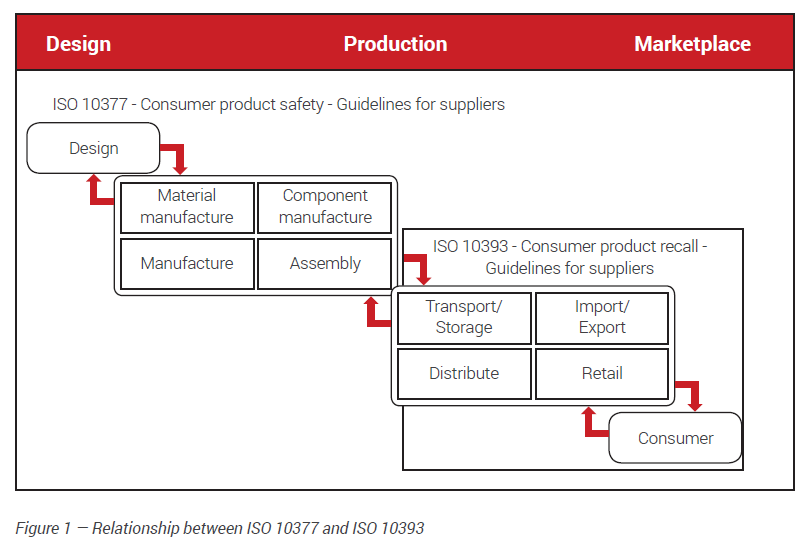
Three key principles that an organization needs to consider when adopting ISO 10377
In order to achieve the best results when creating a product every company should follow three main principles such as:
Safety in design - Safety in design covers the tasks that evaluate safety during the original product design. Through these tasks, the preparation of documents and material that comprise the products technical specification are included. Additionally, the designation of the product life cycle is considered to be a very important issue that needs to be underlined during the design phase. Moreover, during the design phase, it is essential to consider the method used to arrive at a tolerable risk through hazard identification and to determine how consumers are exposed to hazards.
Safety in production - Safety in production refers to the manifestation of design principles and the hazard analysis into the establishment of the actual product. It holds the practical steps necessary to move basic principles along the supply chain, from design to manufacturing.
Safety in the marketplace - Safety in the marketplace covers the responsibilities of the distributor, provider or vendor in assuring that the product order meets the safety requirements. Ensuring safety in the marketplace means that the incidents, warranty returns and all other product hazards that were missed in the earlier assessments will verify conformance and determine the need for continuous improvement.
How to establish a product safety management program?
It is important for a manufacturer to recognize whether they need to establish a consumer product safety management program or not. This program, according to ISO 10377, can be difficult to be established if potential hazards that are involved in the company are not recognized. Thus, the company firstly needs to identify the hazards and evaluate the current situation, and then establish a product safety management program.
As soon as the manufacturer has completed the internal audit, then it can be taken into consideration what will be the most appropriate consumer product safety program for the organization. The final result is based on the level of the hazard that the organization has assessed. It is stated in ISO 10393, that in order to establish a product recall programme a manufacturer needs to have a policy statement that proposes that the products are safe to use. This policy statement is important because it presents the hazards that need to be removed from the marketplace and the concerns regarding health are adjusted.
In addition, it is difficult to accomplish consumer product safety in an organization if the people that are involved in production do not have additional training and responsibility, thus, actions shall be taken to provide training, and to identify and explain the roles and responsibilities of the recall management team.
Product Safety Committee
After the identification of roles and responsibilities a product safety committee should be set. Individuals from different departments should be involved to establish guidelines and criteria for assessing risk within the organization, review design, create warning and labels, advertise brochures and create policies in regards to consumer product safety.
Techniques on Measuring Product Safety
After completing the internal audit and risk assessment a manufacturer is prepared to establish a safety program. The manufacturer needs to ensure that the employees are following the rules and regulations that were set during the previous phases. In order to measure the product safety the following techniques should be followed: implement the established policy, analyze the products when they are in the conceptual stage, implement corrective actions to prevent reoccurrence, and structure a continual improvement phase.
Conclusion
There are varieties of products in the global marketplace that are recognized to be safe yet, many people get sick or die from them. It is important for a manufacturer to establish a product safety management program by adopting ISO 10377 and ISO 10393. These international standards focus on consumer product safety, reducing risk and if necessary implementing a product recall. Through these international standards, a manufacturer will be able to assess risk and help suppliers to implement a product safety management program.
Author:
Suzana Ajeti is the Senior Manager of the Trainer Program and Auditor Program processes at PECB. She is in charge of the recruiting, evaluating and certifying process of potential candidates in both programs. If you have any questions, please do not hesitate to contact her at: marketing.hse@pecb.com.